Welding is the process of joining two pieces of metal together. But there are many types of welding to achieve this. There’s no such thing as the “best type of welding”— it depends on the materials and application, and also on the needs of the manufacturer.
It’s important to select the right method for the job at hand, considering the materials being joined (metals or thermoplastics), the thickness of those materials, and the environment in which the welding will take place, among other things.
Automated Welding
Automated welding, more commonly known as robotic welding, uses electronically controlled tools and equipment to complete welding tasks with minimal human oversight. In the right applications, robotic welding systems can significantly improve quality, productivity, and profitability for a manufacturer.
As welding automation technologies become increasingly efficient, versatile, and affordable—and the shortage of skilled professionals continues—more manufacturers are expected to integrate automation systems into their welding processes.
Benefits of Automated Robotic Welding
In the right applications, robotic welding systems offer a number of benefits, including:
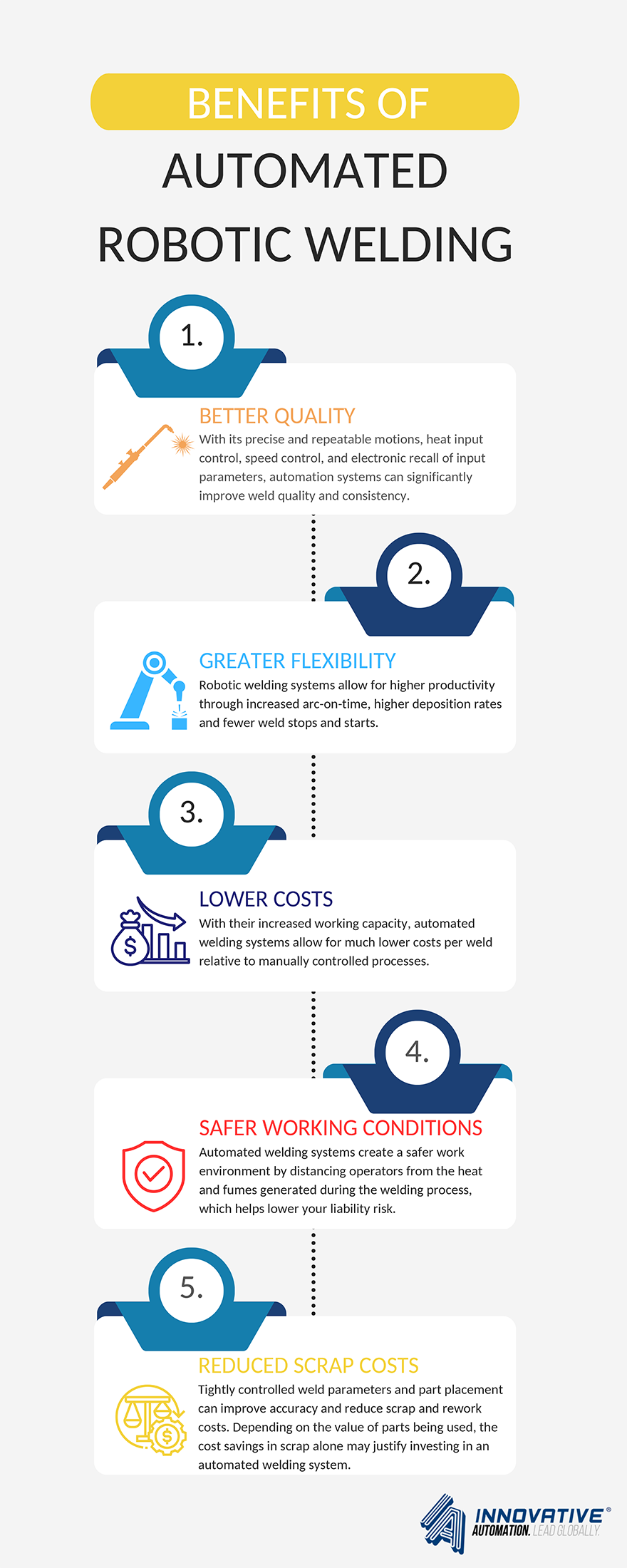
Best Applications of Automated Robotic Welding
Automated robotic welding is used for easily repeatable processes with high volume. It is successfully used in many applications across a wide variety of industries. Two key factors to consider when deciding if your operations are a good candidate for a robotic welding process are:
1. WELDING TASKS PERFORMED
While robotic welding systems are great for simple and repetitive welds at high speeds, joining parts with gaps or hard-to-access locations can present some challenges. An automation solutions provider can help you determine if your operations are suitable for robotic welding systems.
2. PRODUCTION VOLUME
Since one of the key benefits of robotic welding is the ability to quickly perform high volumes of welds, it’s important to make sure your production volume is large enough to justify the initial investment. That said, as robotic welding systems become cheaper and more accessible, even small manufacturers may find it’s worth the upfront cost.
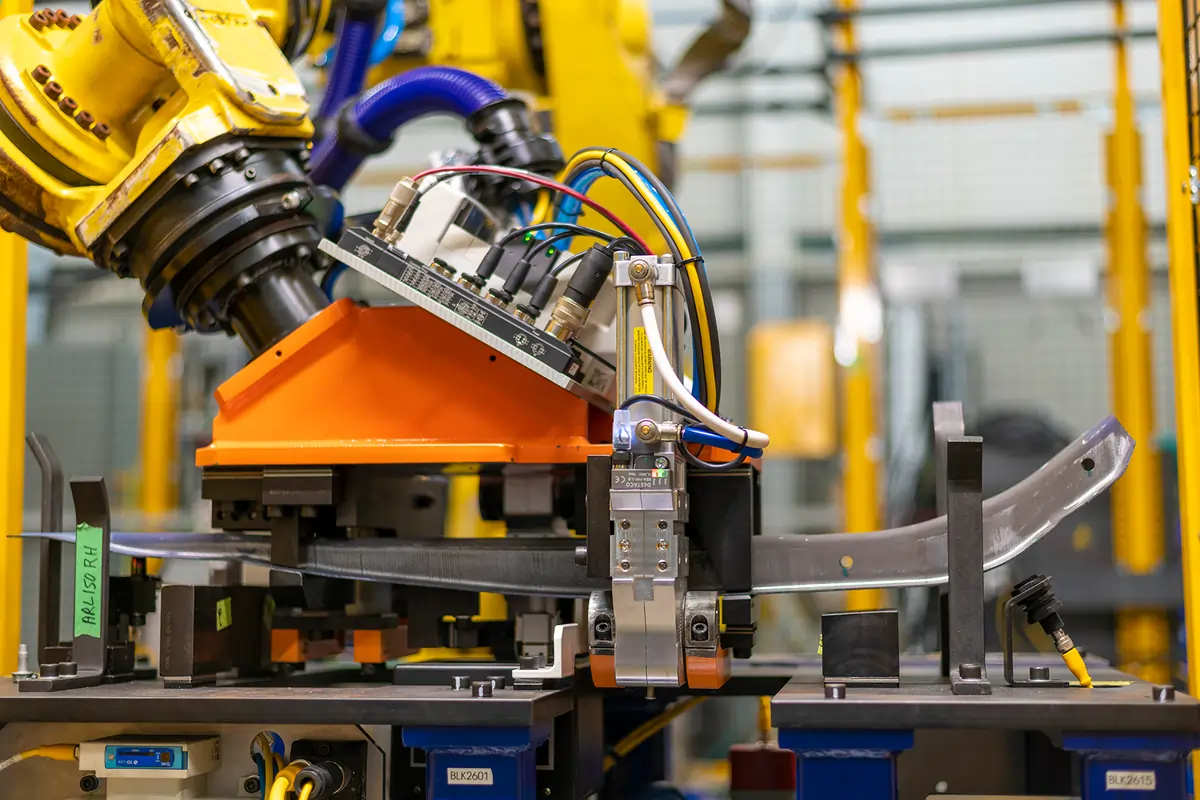
Robotic Welding Systems
Robotic Tig Welding
Some key benefits of robotic TIG welding include:
- Precise heat control and exact penetration results in improved weld quality.
- On-the-fly procedure adjustment for automatic switching of procedures between thick and thin materials.
- Torch movement and automated control of the welding variables such as preflow, upslope time, welding amperage, and pulse frequency.
- Arc length is automatically maintained with automatic voltage control (AVC).
- Tightly controlled bead width, penetration, and surface appearance.
- Improved welding productivity—between 100 and 300 percent—reduced operator training time, and reduced inspection costs.
- Ability to save welding schedules and welding programs for easy retrieval.
- Lower initial investment compared to robotic laser welding systems.
Robotic Laser Welding
Robotic laser welding systems use programmable robots incorporated with advanced optics to precisely target an area on the part being welded. Some key advantages of robotic laser welding include:
- High weld quality and uniformity thanks to low heat input and precise laser power control.
- Between three and ten times faster than other robotic welding systems, such as robotic TIG welding, allowing for low unit costs.
- On-the-fly adjustment for spot position, laser power, and beam diameter, allowing for unprecedented flexibility in the types of materials and thickness one can process.
- Not limited by given wire diameter as with arc welding processes — the ability to go from micron-thick materials (e.g. battery foils) to large cross-sections requiring deep penetration welds.
- Lower heat input and a smaller heat-affected zone around the weld mean fewer instances of distortion or metallurgical changes that weaken the weld.
- Suitable for a wide variety of materials, including aluminum, titanium, stainless steel, carbon steel, and even precious metals like gold and silver.
- Versatility allows welding material combinations that other robotic welding systems can’t join.
- Ability to use a single welding head or cell for multiple jobs or multiple parts of various materials.
What’s inside a robotic laser welding cell?
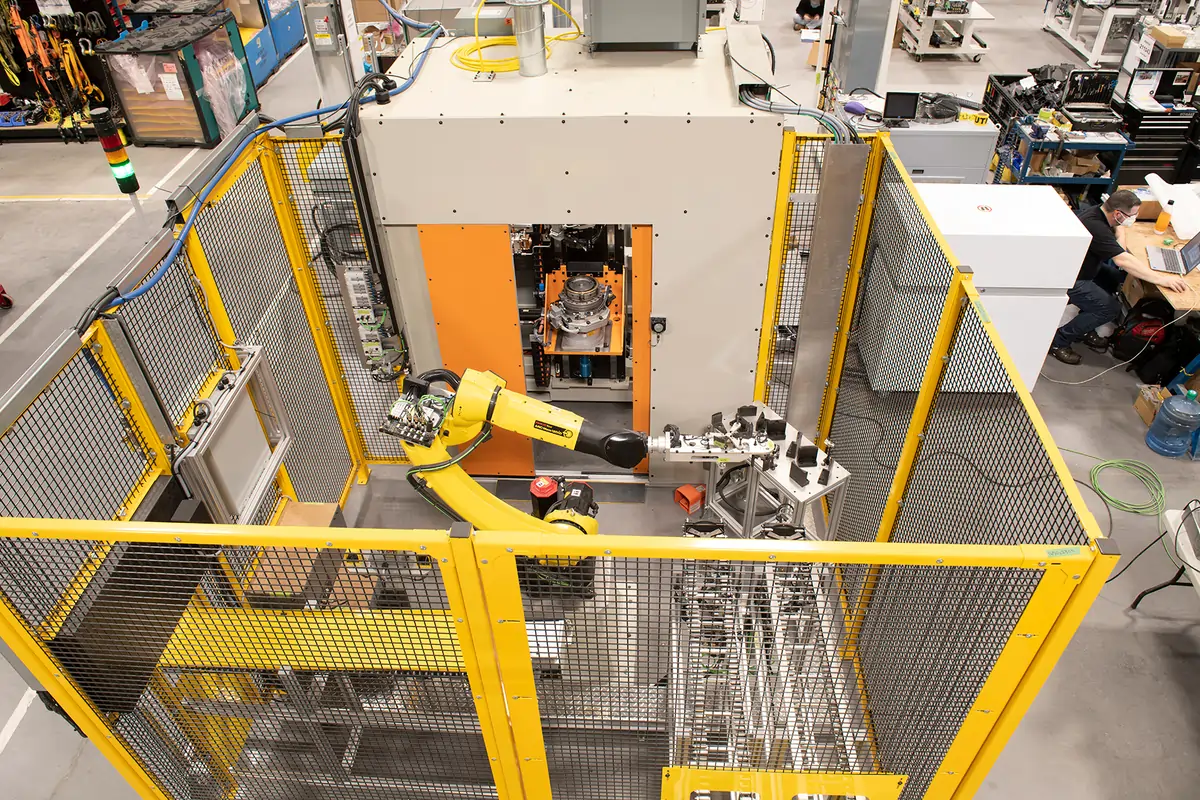
- The Workcell: Metal barriers form an enclosure to effectively block glare and other welding hazards that could endanger workers on the production floor. Workcells often include safeguarding features like safety scanners, lock-out/tag-out systems, live-man switches, light curtains, and glare shields.
- The Robot: The welding robot, which includes its mechanics and controls, is the central component of the weld cell. It moves and operates the controls of the laser directly. Robot models have different design characteristics. When selecting your robot, consider factors like reach, payload capacity, speed, and precision.
- The Laser: There are three primary types of lasers used in the laser welding process: gas (CO2), solid-state, and fibre. Regardless of the type of laser, the laser system generates the welding beam. It includes the head and the power generator, sometimes as separate components.
- Cooling System: Lasers generate massive amounts of heat, which can damage internal components, which is why most laser types require a cooling system to function. Cooling systems keep laser temperatures within a functional range, so most robotic laser welding systems will include one.
- Parts Presentation Framework: How will you present the part to the robot for welding? Will you use conveyors, jigs, turntables, clamps, or something else? There are many options available for laser welding systems. Most automation companies will work with you to choose the best option for your operations.
- Sensing/Monitoring System: Temperature sensors and safety equipment are standard in robotic weld cells, and beam and seam trackers are also common. Automation companies often configure packages with vision systems for quality control/inspection, safety, and thermal monitoring applications.
Choosing an Automation Systems Supplier
Mecsmart, a world-class manufacturing automation provider for the automotive, industrial, commercial, service and assembly sectors, works collaboratively with clients to create automation solutions tailored to their applications and processes. We provide a range of automation solutions, including:
- robotics process automation
- automation tooling systems
- material handling systems
- force testing
- electrical design
- industrial control systems
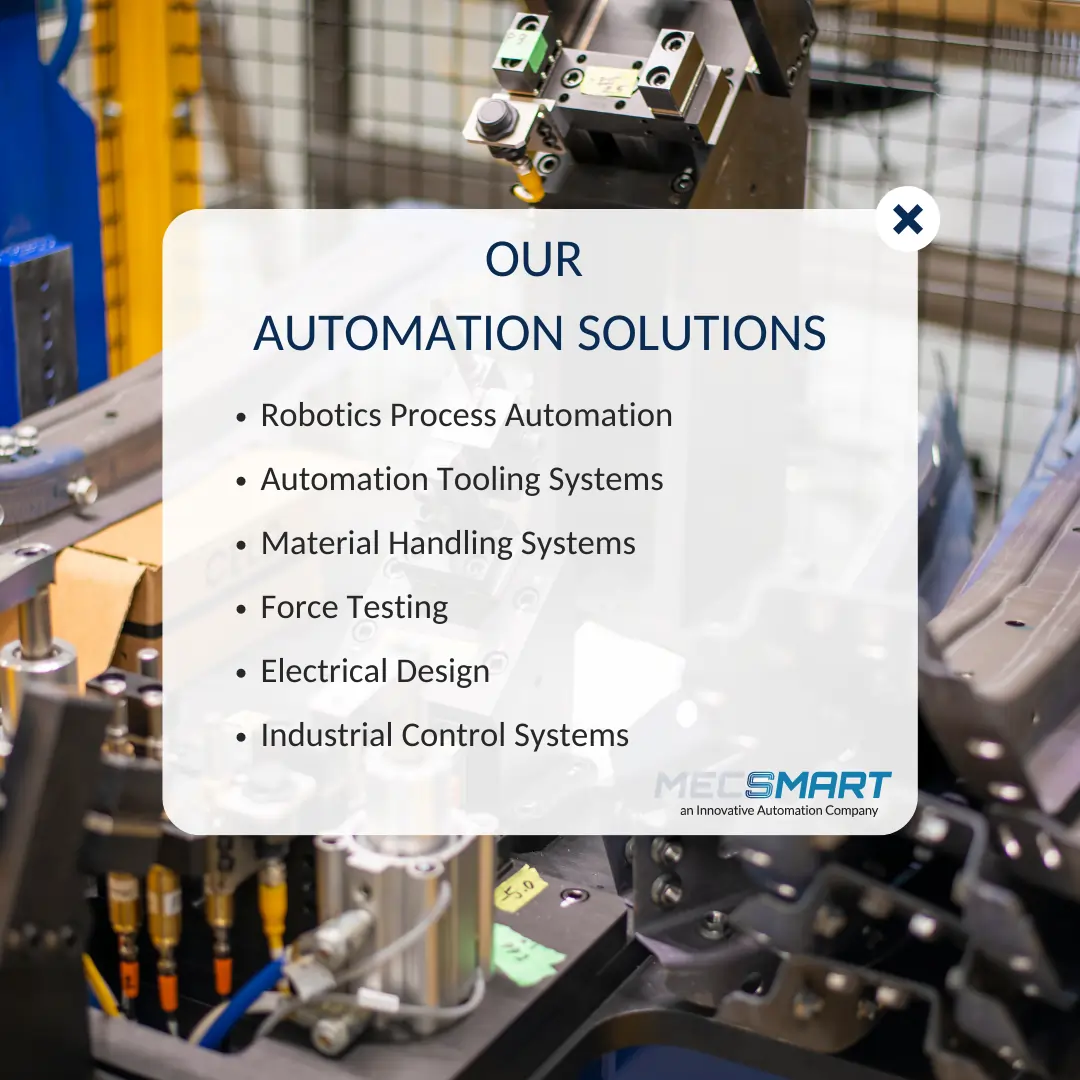
Our technicians and engineers are at the forefront of today’s industrial most advanced manufacturing technologies. We also have the best customer support in the industry, providing servicing for all the equipment we build, and phone support for troubleshooting.
We understand that 10 minutes on the phone with our experts could save you hours of troubleshooting at your facility, and our mission is to make your life easier. Learn more about the Innovative Automation family of company’s robotic welding automation services.
The Mecsmart Process
Starting with Concept & Application Planning, our Design team will work with you to develop the best design concept to suit your application, while keeping cost-efficiency, operator ergonomics, up-time, and serviceability top-of-mind.
Next, our Engineering team will develop a detailed process plan for every new job to refine the design intent further, and we’ll regularly review the designs with you throughout the design process to make sure it’s meeting your requirements. Once you are 100% satisfied with the design, our Machine Build & Development team works to bring it to life.
Our Electrical and Software Engineers develop and design all control systems in-house. All controls are hard-wired on our shop floor, and every system is tested on the premises. Once the job is complete, we provide a detailed operations manual for each job that offers a spare parts list, all vendor-supplied documentation, and maintenance and service requirements. Learn more about our machine build and development services.
Don’t hesitate to get in touch with us to learn more about Mecsmart, and how we can help you work smarter, better, and faster.
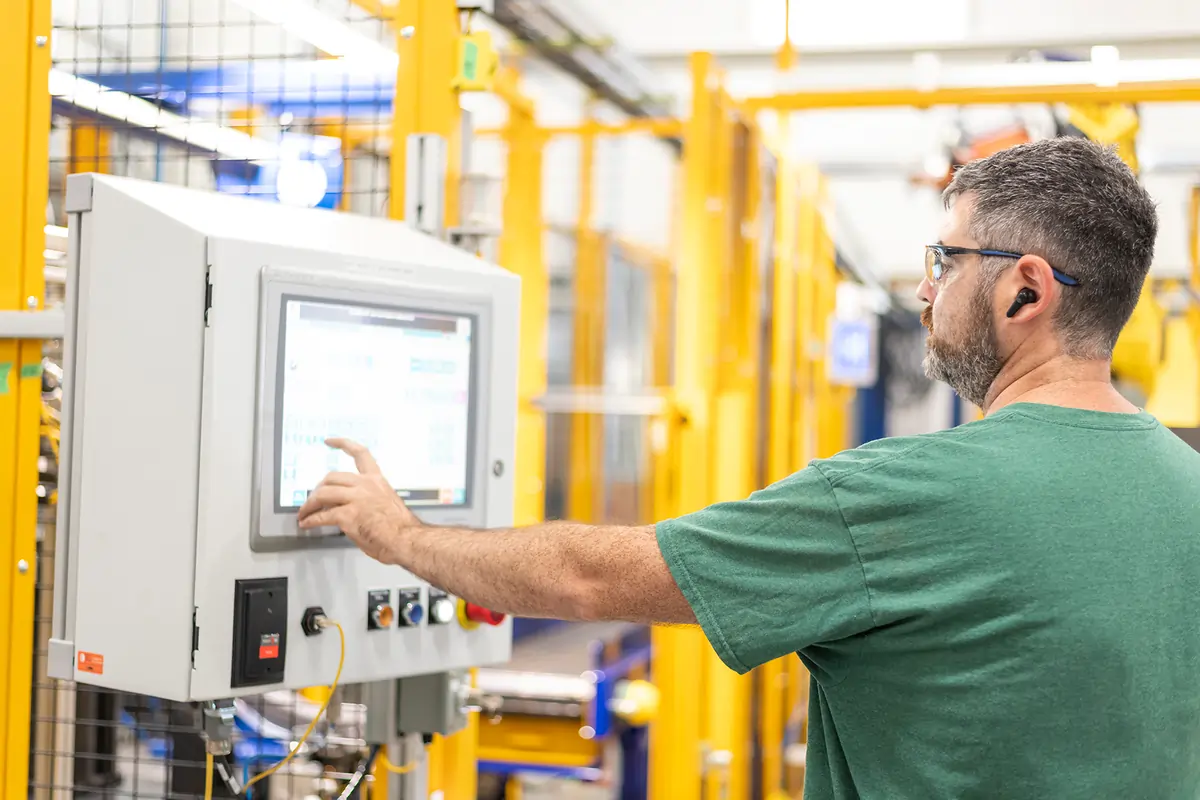